27
2023
-
10
It turned out to be him! The original Chinese technology that subverted the printing and dyeing industry was born, and perfect "dyeing" will not produce a drop of "sewage"
Xinjiang is China's main cotton producing region, with more than 90% of the country's cotton production here. Although the raw materials of the textile industry are readily available, because the traditional printing and dyeing industry has the disadvantages of large water consumption and large sewage discharge, Xinjiang, which is short of water resources and fragile ecology, has long been unable to develop large-scale printing and dyeing industrial projects, and a large number of cotton raw materials can only be sent to coastal areas for dyeing treatment, and it is difficult to form a whole industrial chain from textiles to clothing.
Author:
Xinjiang is China's main cotton producing region, with more than 90% of the country's cotton production here. Although the raw materials of the textile industry are readily available, because the traditional printing and dyeing industry has the disadvantages of large water consumption and large sewage discharge, Xinjiang, which is short of water resources and fragile ecology, has long been unable to develop large-scale printing and dyeing industrial projects, and a large number of cotton raw materials can only be sent to coastal areas for dyeing treatment, and it is difficult to form a whole industrial chain from textiles to clothing.
In the Shanghai Engineering Research Center for Cleaner Production of Textile Chemistry of Shanghai University of Engineering Science, the scientific research team led by Professor Wang Jiping carried out technical research and developed original technologies with independent intellectual property rights in China, finally reversing this situation. They cooperated with relevant enterprises to build an annual output of 5,000 tons of bulk cotton dyeing demonstration line in Aral City, Xinjiang, since the trial operation in May, under the condition of unchanged product quality such as Color Fastness, not only the whole process operating cost has been reduced by 5%~10%, but also the production process will not produce a drop of wastewater, completely subverting people's conventional perception of high pollution in the printing and dyeing industry. This move not only provides an effective solution for the large-scale development of the printing and dyeing industry in Xinjiang, but also becomes a turning point in the development of China's printing and dyeing industry.
How to make the printing and dyeing industry achieve low-cost clean production? What are the features of this original technology? With these questions, the reporter came to Shanghai University of Engineering Science a few days ago.
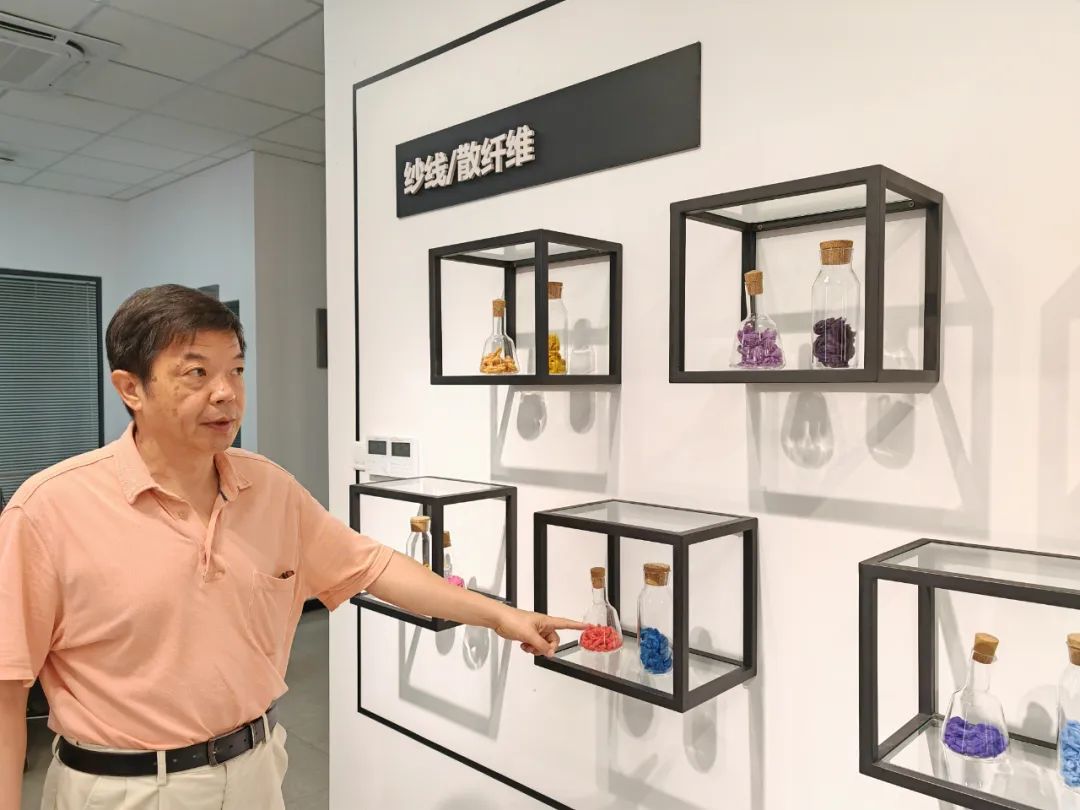
Professor Wang Jiping, who told reporters about the technical principle
Why is the traditional printing and dyeing industry "unpopular"?
In 1982, Wang Jiping entered the Department of Textile Chemistry of the former China Textile University (now Shanghai Donghua University) and began his master's studies. After graduation, he stayed on to teach. In the late 80s of the 20th century, Wang Jiping also joined the overseas boom, in 1994 he received a Ph.D. in organic and polymer chemistry from the University of Texas at Arlington, then joined Procter & Gamble, and began to serve as the chief scientist of P&G's global textile and industrial standards department in 2005. In 2011, in order to realize his scientific research ideals, Wang Jiping returned to China to work. In 2019, he entered the School of Textile and Apparel of Shanghai University of Engineering Science, and established the Shanghai Engineering Research Center for Cleaner Production of Textile Chemistry, continuing to carry out basic and applied research work.
"China's textile and garment industry is the world's livelihood support industry, with a scale of up to 10 trillion yuan. The printing and dyeing industry is an indispensable part of it, and its industrial scale is as high as one trillion yuan. We can't just wear white clothes, color is a must-have, but because the printing and dyeing industry has a large amount of sewage discharge, many local governments strictly control it. In order to protect the environment, some areas will even order some printing and dyeing enterprises with relatively large pollutant emissions to shut down and transfer, carry out the 'cage for bird' of industrial land, and introduce more environmentally friendly high-tech enterprises on the original land. Wang Jiping said.
Why does the printing and dyeing industry have a large amount of sewage discharge?
Wang Jiping held a red cotton cloth and explained: "70% of Chinese cotton fibers need to be dyed, 50% of polyester fibers need to be dyed, and the main task of dyeing cotton fibers is 'reactive dyes'." Reactive dyes, also known as reactive dyes, are a new class of water-soluble dyes that appeared in the 50s of the 20th century. Reactive dye molecules react with hydroxyl groups in cotton cellulose and amino groups in protein fibers to form covalent bonds. Reactive dyes have the characteristics of bright color, good uniformity, high color fastness, complete chromatography, and low cost, but a major problem of reactive dyes is low dye utilization, high water consumption and high amount of salt consumption compounds. Therefore, the dyeing water containing high salt and high organic matter is polluted. ”
Wang Jiping further explained that in fact, the two materials of reactive dyes and cotton fibers placed together in water are "mutually exclusive", and both carry a large number of anions. Although cotton fibers will swell up with the help of water, making it easier for dyes to enter, reactive dyes are more "preferred" to water. At this time, sodium sulfate, a salt compound, is needed to "help" to neutralize the anion of the dye and the fiber, so that the dye "obediently" "enters" the fiber. The water and salt consumption of this process is enormous. He calculated an economic account to reporters: "To complete the dyeing (dark color) of 1 ton of cotton fiber, 100 tons of water and about 1 ton of sodium sulfate are required, and the dyeing efficiency of general reactive dyes in the water bath is 60%~70%. When the dyeing is completed, a large amount of water washing is also required to ensure the color fastness of the qualified product, and 100 tons of wastewater is generated from this, which requires back-end treatment and discharge. Contaminants in wastewater include reactive dyes after hydrolysis, large amounts of sodium sulfate, and impurities such as various organic matter on cotton fibers. ”
Inspiration for dry cleaning "color crossing"
Can "dyeing" be done without a lot of water and salt?
In 2002, while working at Procter & Gamble in the United States, Wang Jiping was inspired by a chance work experience, when he was in charge of the development of an environmentally friendly dry cleaning technology. The advantage of dry cleaning is that clothes of various colors can be washed together without color crossing; However, Wang Jiping found that if a small amount of moisture is mixed in the dry cleaning solvent, serious color crosstalk will occur, even more serious than washing color crossing.
Wang Jiping, who has a background in textile dyeing and finishing, suddenly "clicked" in his heart, and he instinctively realized that this may be a completely new textile dyeing technology path. Since Procter & Gamble's main business focuses on washing and rarely involves textile dyeing technology, Wang Jiping entrusted university classmates working at Zhejiang Sci-Tech University to start basic research work on non-aqueous less water dyeing. In 2011, Wang Jiping gave up the preferential treatment abroad and resolutely returned to China to carry out research work, he completed the feasibility study of laboratory to pilot technology at Zhejiang Sci-Tech University, and led the team to participate in the local entrepreneurship competition. Their entrepreneurial plan won the first prize of the 2nd "Rising Tide Orient Win in Haining" Entrepreneurship Competition in Haining, and then won the Winner Award of the 7th China Innovation and Entrepreneurship Competition. The team led by him established Zhejiang Lvyu Textile Technology Co., Ltd. in 2014 and began the exploration of industrialization of scientific and technological achievements.
In 2019, Wang Jiping came to Shanghai University of Engineering Science to continue his research and development work. Shanghai, which is building a global science and technology innovation center, embraced this returnee student, giving him a more efficient scientific research platform and broader development opportunities for industry-university-research docking.
At that time, a commander of the Xinjiang Construction Corps made a special trip to Wang Jiping, hoping that he could help solve the problem of discharging local high-salt dyeing sewage, make large-scale cotton textile dyeing possible, provide technical solutions for opening up the whole textile and garment industry chain in Xinjiang, and help solve the problem of local employment difficulties.
With the strong support of the leadership team of Shanghai University of Engineering Science, Wang Jiping led the team to start the journey of scientific and technological aid to Xinjiang.
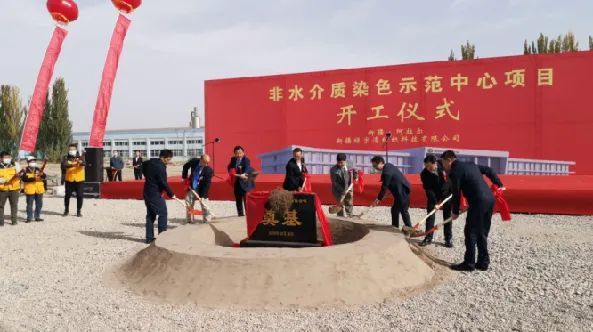
The picture shows the groundbreaking ceremony of the Xinjiang base
In the depths of the desert, the major problem of "zero sewage discharge dyeing" of cotton fiber was overcome
Carrying his bags, Wang Jiping led his team to the depths of the desert. A dyeing factory that does not produce wastewater was born thanks to their efforts.
"This is a new set of technical paths, the biggest features are that there is no salt compound, no waste water is generated, and the dye utilization rate is particularly high." Wang Jiping described the working principle of "less water and no salt in non-aqueous medium, zero discharge and dyeing of sewage".
In fact, the principle of dry cleaning is equivalent to the chemical "extraction" principle, which is a washing method that washes clothes with liquid organic chemical solvents (such as tetrachloroethylene, hydrocarbon solvents, etc.) to remove oil or stains.
"Our method is to add a small amount of water and the reactive dye needed to the dry cleaning solvent. The dye does not dissolve into the hydrophobic dry cleaning solvent, only into a small amount of water droplets, and in professionally designed dyeing equipment, the water droplets dissolved with the dye will be in uniform contact with the non-aqueous medium and cotton fiber. To know that cotton fiber is a hydrophilic fiber, they especially 'like' the 'water droplets' with dye, will gradually grasp the dye during the dyeing process, complete the reaction with the dye, the utilization rate of the dye can be as high as 90%. In this technical path, the whole process of dyeing does not require the addition of the salt compound sodium sulfate, and the affinity of water droplets and fibers can be used to complete the dyeing. Wang Jiping said.
The reuse process of non-aqueous media and water is also very unique. Wang Jiping said that after the dyeing is over, a small amount of water is added to clean the cotton fiber, and then the treatment process of non-aqueous medium and water residue. The first step is oil-water separation, and the dry cleaning solvent-based dyeing media involved is hydrophobic and easy to separate from water with dye. The second hurdle is to set up a nanofilter membrane to block the organic matter and hydrolyzed dye brought by the washed cotton fiber, so that water molecules with sodium sulfate can pass through. The third hurdle is to set up a reverse osmosis membrane, which can separate sodium sulfate, a salt compound and water molecules. Finally, a small amount of "concentrated wastewater" enters the distillation mode, becoming a small amount of solid waste and a part of clean and hygienic distilled water.
The huge amount of wastewater problem that has existed in the printing and dyeing industry for a hundred years has been easily solved by Wang Jiping. He said: "Others need 100 tons of water to dye 1 ton of cotton fiber; We only use 0.25 tons of water, reducing the dyeing time by 20%. A drop of wastewater will not be generated during the whole dyeing process, and the solid waste produced can be incinerated or landfilled, and can also be used as fertilizer and bricks, and the recycled water produced can be used in the next dyeing. Since the dyeing process requires steam heating, generating condensate, our factory not only does not need to use a lot of water, but also produces some excess distilled water for watering the flowers. ”
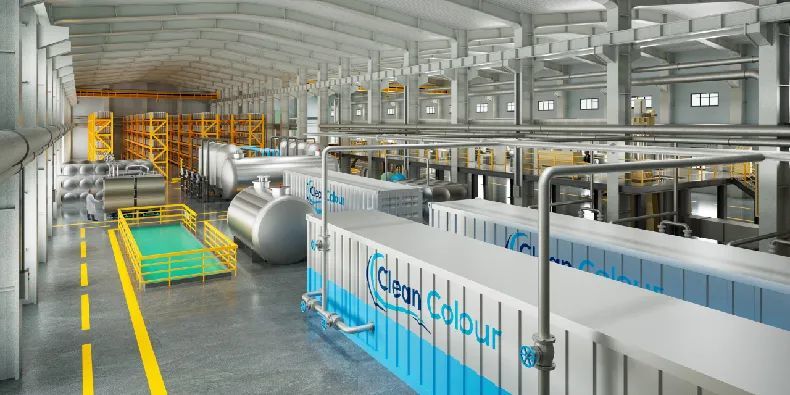
The picture shows the media recovery and water recycling system on the Xinjiang demonstration line
At that moment, colleagues in the textile field in Xinjiang gave him a thumbs up from the bottom of their hearts. In the past, a large amount of wastewater after dyeing was directly discharged into the depths of the desert, and since the national energy conservation and emission reduction policy was issued, the local printing and dyeing industry has been pressed the pause button, because it is no longer possible to "go through" from the perspective of water consumption and sewage discharge; Wang Jiping's team turned the highly polluting production process into a "clean production" working mode. After the completion of the overall technical route, compared with the traditional route, it can also save 5%~10% of the production cost.
Find a new route for polyester fiber "anhydrous dyeing" technology
In China's textile industry, there are two major fibers: one is cotton fiber, and the other is polyester fiber that uses more energy. Data show that China's polyester fiber usage accounts for about 70% of all textile fiber materials.
The water consumption of traditional polyester fiber dyeing is also amazing, and it takes about 40 tons of water to complete the dyeing of 1 ton of polyester fiber. Wang Jiping said that the principle of polyester fiber dyeing and cotton fiber dyeing is different. Polyester fibers are hydrophobic, they hardly swell in water, and the reactive dyes used for dyeing cotton fibers cannot penetrate them. Therefore, the traditional technical route will generally set the dyeing temperature at about 130 degrees Celsius, at this temperature, the polyester fiber will have thermal expansion, and the disperse dye that is not dissolved in water exists in the form of granules, at which time the disperse dye will "run" into the inside of the polyester fiber. When the temperature drops, the expansion of the fiber ends, which envelops the dye particles inside the fiber. However, at this time, there are still many surface dyes left on the polyester fiber, which need to be rinsed with a large amount of water. Because the use of polyester fiber in China's textile industry is much higher than that of cotton fiber, in terms of the amount of sewage discharged after dyeing, polyester fiber dyeing greatly exceeds cotton fiber dyeing.
In fact, many scientists want to break through the traditional process of polyester dyeing and develop a clean and environmentally friendly process route. In 1989, E. Schollmeyer, the Northwest Textile Research Center in Germany, invented the process of supercritical carbon dioxide dyeing. Any kind of gas, at critical pressure and critical temperature, will become a fluid, this fluid has very unique physical properties, its viscosity, high density, good flow, mass transfer, heat transfer and dissolution properties. German scientists found that in supercritical carbon dioxide, the disperse dye will be fully dissolved by the carbon dioxide fluid, and the process of anhydrous dyeing can be easily completed. The technology has also been listed as a key scientific and technological research project during China's "Eighth Five-Year Plan" period and beyond.
"But to complete the supercritical CO2 dyeing process, the equipment requirements are very high. If you want to maintain the traditional polyester dyeing temperature of 130 degrees Celsius, in theory, it is necessary to build a special equipment that can withstand 250 atmospheres, which is not only expensive, but also has high safety risks in the dyeing process. Chinese companies have introduced relevant manufacturing equipment from Switzerland, but they have found that the dyeing process is difficult to control and the dyeing quality is difficult to guarantee, so they have not been put into actual production at present. At present, there are relevant companies in China that can produce supercritical carbon dioxide dyeing tanks, although the price is lower than foreign products, but it is still much higher than that of traditional dyeing vats. Supercritical CO2 staining has a good 'laboratory' staining theory, but it is not a suitable technique for large-scale staining due to its insurmountable ultra-high pressure characteristics. Wang Jiping explained.
Continuing to explore and practice along the thinking of "dry cleaning and dyeing", Wang Jiping's team found a new type of media in a unique way to realize a low-cost low-pressure anhydrous dyeing process of polyester fiber. He told reporters that this is an organic solvent medium that can ensure the safety of the human body, and its boiling point is about 200 degrees Celsius, which can dissolve a part of the disperse dye. The mixture has a solvent and dye aggregation structure and molecular structure inside, and under conditions close to atmospheric pressure, high-quality anhydrous dyeing can be completed, and the dye use efficiency is as high as 90%. The dyes remaining on the fibers can also be cleaned with this organic solvent, and the solvent medium can be efficiently recovered and recycled. After dyeing and cleaning, as long as the polyester fiber is dried in a closed environment, the dyeing process is completed, and the whole process will not produce a drop of sewage.
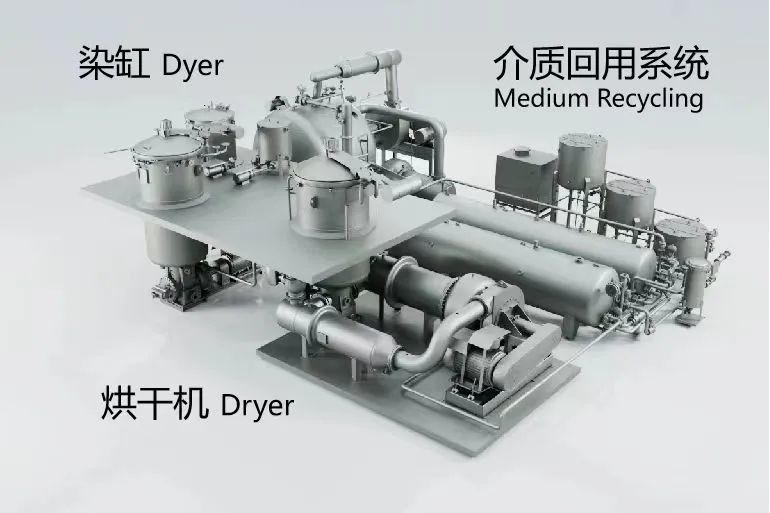
The picture shows a schematic diagram of the low-pressure anhydrous dyeing system
The first production base using this process route has been completed near Hangzhou, and the entire production base does not need to build a sewage treatment station and does not need the government to give sewage discharge targets.
"We are also working on an artificial intelligence operation model, using our dedicated liquid dye and dye additive distribution system, workers can easily develop dyeing recipes in the control room, and can automate the low-cost anhydrous dyeing process with just one button." Wang Jiping said.
In the future, we must strive to remove the "pollution hat" of the dyeing industry
At present, Shanghai Textile Chemical Clean Production Engineering Technology Research Center has comprehensively overcome the zero-discharge dyeing process of hydrophilic fiber and hydrophobic fiber, which can cover almost all fiber dyeing processes, and follow-up research work is still being carried out.
"There are different methods of dyeing, you can do fiber dyeing at the front end and then spin the weaving cloth, or you can dye the yarn and dye the cloth at the back end. Of course, the color fastness of front-end dyeing is higher than that of back-end dyeing, and the product flexibility is higher. Wang Jiping explained.
Wang Jiping's scientific research team has also achieved a breakthrough in the non-aqueous medium rolling and dyeing of cotton cloth. The team carried out production, education and research in relevant enterprises in Xiaoshan District, Zhejiang Province, and finally completed the entire process construction, "dyeing 1 ton of cotton cloth, only 7 tons of water, at the same time can recycle this water, no wastewater discharge problems, only some low-pollution solid waste remains." Wang Jiping revealed that the team is currently helping related enterprises build large-scale production lines for cotton cloth "non-aqueous medium rolling and dyeing technology" in Nantong, Jiangsu Province.
For the waterless dyeing technology of polyester fabric, the team is still continuing to tackle the problem, striving to overcome this production problem in the near future and continue to expand the process boundary of low-pressure anhydrous dyeing.
Wang Jiping said that his biggest wish is to remove the highly polluting "hat" of China's printing and dyeing industry and upgrade and replace the existing industry.
"The traditional printing and dyeing industry consumes serious water resources, has a large sewage discharge and is difficult to treat. More than 10 years ago, the relevant departments formulated pollution emission indicators, which met the needs of energy conservation and emission reduction at that time, and indeed improved the environment. However, at present, it has reached the era of comprehensive technological upgrading, and the key technologies of green, low-carbon, salt-free non-aqueous medium/anhydrous dyeing and zero sewage discharge have fully verified the technical feasibility and economic feasibility of large-scale promotion after 16 years of research and development. Our goal is no longer to simply reduce emissions, but to upgrade the entire industry to a clean industry with zero effluent discharge. Cleaner production and sustainable innovation are the only way for the development of China's printing and dyeing industry, and this new printing and dyeing technology can bring high value-added economic benefits to the textile production area nearby. Wang Jiping said.
But at present, the promotion of technology seems to have encountered barriers. "In the national industrial catalog, the traditional printing and dyeing industry is listed as a 'restricted' industry due to its high pollution and high energy consumption. Although green, low-carbon, salt-free non-aqueous medium/anhydrous dyeing and zero sewage discharge technologies can provide systematic solutions for the industry, policy restrictions hinder the promotion of innovative technologies. Wang Jiping called on relevant national departments to open up a development path of ecological innovation and development for textile printing and dyeing enterprises, "As long as enterprises can not discharge sewage, do not want sewage indicators, relevant departments should encourage and support printing and dyeing enterprises in terms of industrial positioning, environmental impact assessment, energy assessment, and funds." We also look forward to contributing to the sustainable development of China's textile and apparel industry." ”
Source: Shanghai Science and Technology News, Ketan Spring and Autumn
Key words:
Related news
undefined